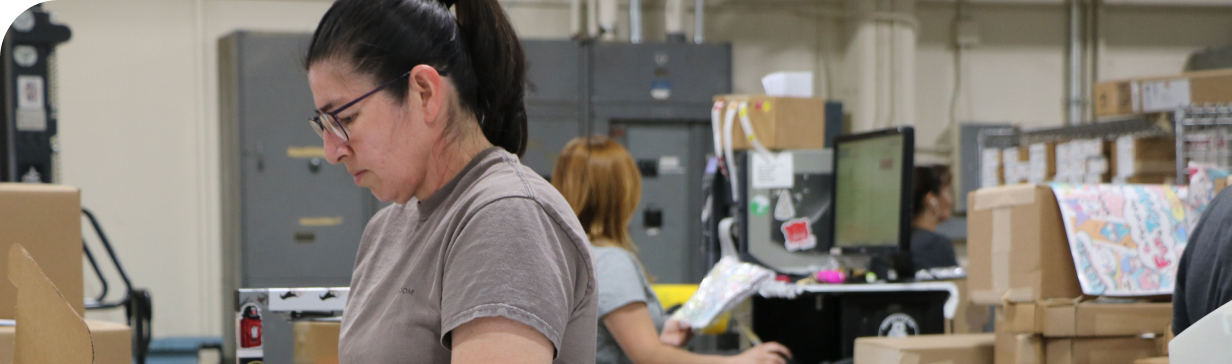
The 3 Main Stages of Quality Control in Printing
Estimated reading time: 5 minutes
Quality control is a cornerstone of printing perfection and it’s a painstaking process that touches every stage of printing. It’s through strict quality control measures that printing specialists are able to ensure that every job is subject to the company’s standard for excellent prints, the equipment is prime and ready for printing, and that every run is documented so that operators and clients alike can learn from them. In this article, we will learn about the quality control measures taken by printing specialists and how they enforce these standards throughout the printing process.
Stage 1: Prepress Quality Control
When it comes to printing, quality assurance begins way before the presses heat up. As soon as printers get a job order, prepress begins — a multistep procedure crucial to ensuring the accuracy and readiness of the file to be printed. Prepress has three phases — preflight, proofing, and platemaking.
- Preflight. Just like pilots would conduct routine checks prior to every flight, printing specialists live by a checklist filled with items that need to be ticked off as the file is being prepared. The preflight stage involves checking for details such as typeface and fonts files, bleed and crop marks, and color models particularly if the colors have been converted from RGB to CMYK. It is common practice for printers to work with the client during the preflight stage especially with proofreading, checking of prices wherever applicable, and making sure hyperlinks and QR codes are working.
- Proofing. At the proofing stage, printers generate high-quality proofs of the file and send these to the client for checking of colors and layout and then proceed to approval. There are two types of proof — soft proof and hard proof. Soft proof refers to the digital format, typically in PDF, which the printer emails to clients, while hard proofs are physical prints that are often sent via post. When the proof is approved, the printing begins. If the client isn’t satisfied with the proof, the file will be updated and will undergo the approval process again until it's free of errors.
- Platemaking. This step in prepress stage is where the approved design is transformed into physical metal or polymer plates. These plates are used to transfer the ink from the printer to the substrate or paper, a method commonly used in offset printing which is ideal for printing big quantities.
The UPrinting Upside: At UPrinting, we implement an exhaustive checklist to guarantee that your file is print-ready. We love paying attention to the minute details including image resolution, artwork size, bleed and safety zones, and color settings to ensure that your file is faultless and will print correctly.
Stage 2: In-Process Quality Control
This stage of quality control is highly technical and relies heavily on the capabilities of printing experts overseeing the print job. Apart from inspecting the file about to be printed, printing specialists perform routine checks on the printer, finishing machines, and other equipment that will be used for the job. Any modifications to the printers, inks, and substrates are also finalized and consistently monitored.
- Checking of First Batch of Prints. It’s customary for professional printers to check the first run of prints and inspect it for any issues or see if the prints match quality of the approved proofs. It’s also up to the specialist in charge to decide whether to proceed with printing the rest of the quantities or if there are changes that need to be applied before printing another run.
- Adjustment and Troubleshooting. Printing specialists also inspect the first run for any inconsistencies, correct any errors and make necessary adjustments to the machines before printing the succeeding runs.
The UPrinting Upside: We keep our eyes peeled. To ensure that every print run is up to the standards of our predetermined settings, we supervise every step pf the printing process and make sure that the machines are working perfectly, the ink doesn’t budge, and the substrates don’t run out. We also check the output and the equipment at every stage of production which covers each print run, supplies availability, and overall product quality.
Stage 3: Post-Printing Inspection and Finishing Quality Control
At this stage, printing is completed and is prepared for delivery. Depending on the supplier, it is possible for some printers to involve the client in checking the prints to inspect colors, sizes, and shapes, as well as finishing details such as binding, coating, or numbering.
- Sorting Prints and Separating Rejects. A printing specialist goes through each print run carefully to separate the rejected prints or those that didn’t meet the standards of the final design.
- Finishing. Print products often go through several stages of finishing processes before they are considered ready for delivery. These may include cutting, folding, binding, and laminating, and it’s also the job of printing specialists to oversee these methods and ensure that the finishing machines are set up correctly just like with printing.
- Record Keeping. Part of the meticulous quality control process is documenting notes on the changes and decisions made throughout the production of the prints. Printing specialists also record printer settings, ink level adjustments, and color matching documents and archive these documents for future reference.
- Inspection and Handover to the Client. Printing specialists go over the finished prints one last time before packing them and delivering them to the client.
- Quality Audit and Improvement. Based on the documentation of the printing job, the printer will conduct an internal review of their processes, policies, or procedures and recalibrate as needed. It’s also good practice to request feedback from clients so that the printer can reevaluate the quality of their work.
A printing specialist’s job is to enforce the painstaking job of quality control so that every print job comes out perfectly from prepress to delivery. At UPrinting, we are lucky to work with experts who do not only have a keen eye for quality but are also masters at executing steps that guarantee consistent and excellent print products at every run. We also take pride in our excellent customer service team that’s always ready to walk clients through the printing process starting from the intake and in providing after-sales service.
Find Print Inspiration in These Stories:
- Color Spaces and You: Why You Need to Change RGB to CMYK for Print
- Poster Printing Design Basics
- Peach in Print: How SMBs Can Incorporate Peach Fuzz Into Their Print Materials
At UPrinting, we bring your brilliant ideas to life through exceptional printing services. With seven printing facilities across the US, each staffed by a team of seasoned printing experts using state-of-the-art printing technologies and a comprehensive 33-point print check process, UPrinting is a printing company you can definitely trust.